trap steam d60f cast dsc thermodynamic steel Acu$QT)`/\-FCWf4PF,DqP4$?H:W9SI!

We said that we have 50 psi down here at the inlet and we said were going must zero psi down here at the outlet.
enercon To get the most accurate diagnosis, maintenance personnel should integrate conductivity readings with temperature. In any case, steam traps and systems must be rated for the temperature and pressures of the system.
valves globe gate bonnet union instruments In the case of most mechanical type traps, it is the size of the orifice, not the size of the connection port, that determines the discharge capacity.

0000003534 00000 n
However, for the trap to operate at the same pressure differential, this would require a proportionally larger float, which would in turn increase the size of the trap body. Piping design should be in accordance with ASME B31, which covers the standards for pressure piping. Trap must be installed in upright position to function properly. Any cookies that may not be particularly necessary for the website to function and is used specifically to collect user personal data via analytics, ads, other embedded contents are termed as non-necessary cookies. Steam traps located at the outlet of process equipment serve the same general purpose as drip traps, but the overall intent is to confine the steam within the heat transfer equipment until the steam has released all its latent heat and condenses to condensate. After condensing the steam, the best method to improve steam system efficiency is to return the maximum quantity of condensate to the boiler plant for reuse in the production of steam. Eventually, the steam is bled off through a small hole in the top of the bucket causing it to sink, which repeats the cycle. When steam enters, it fills the inverted bucket causing the bucket to float to the surface which closes the discharge valve, containing the steam in
With an overall understanding of steam traps, it is appropriate to discuss where steam traps are located within a steam distribution system and how trap sizing affects the system. This pulls the disc off the seat allowing condensate to be discharged through the seat orifice located at the top of the trap.
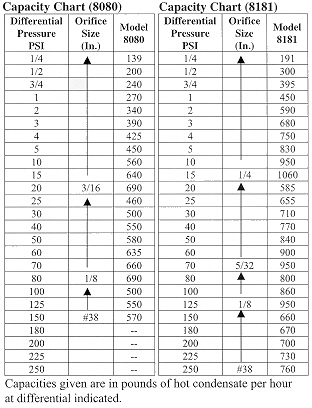
*QeMRx@R,m@X^AxbJ1 C^l'fyS_l+3Ef\
endstream
endobj
311 0 obj
758
endobj
276 0 obj
<<
/Type /Page
/Parent 267 0 R
/Resources 304 0 R
/Contents 305 0 R
/MediaBox [ 0 0 612 792 ]
/CropBox [ 0 0 612 792 ]
/Rotate 0
/Thumb 191 0 R
>>
endobj
277 0 obj
<<
/Count 13
/Type /Outlines
/First 278 0 R
/Last 279 0 R
>>
endobj
278 0 obj
<<
/Title (.1~,7p )
/Parent 277 0 R
/A 303 0 R
/Next 300 0 R
>>
endobj
279 0 obj
<<
/Title ("5U\nqU)
/Prev 280 0 R
/Parent 277 0 R
/A 281 0 R
>>
endobj
280 0 obj
<<
/Title (u$ p')
/Next 279 0 R
/Prev 282 0 R
/Parent 277 0 R
/A 283 0 R
>>
endobj
281 0 obj
<<
/S /GoTo
/D [ 136 0 R /XYZ 79 794 null ]
>>
endobj
282 0 obj
<<
/Title (CHf7[)
/Next 280 0 R
/Prev 284 0 R
/Parent 277 0 R
/A 285 0 R
>>
endobj
283 0 obj
<<
/S /GoTo
/D [ 130 0 R /XYZ 79 794 null ]
>>
endobj
284 0 obj
<<
/Title (Ri`:QB)
/Next 282 0 R
/Prev 286 0 R
/Parent 277 0 R
/A 287 0 R
>>
endobj
285 0 obj
<<
/S /GoTo
/D [ 43 0 R /XYZ -179 827 null ]
>>
endobj
286 0 obj
<<
/Title (=j"yka;^5/)
/Next 284 0 R
/Prev 288 0 R
/Parent 277 0 R
/A 289 0 R
>>
endobj
287 0 obj
<<
/S /GoTo
/D [ 124 0 R /XYZ 79 794 null ]
>>
endobj
288 0 obj
<<
/Title (xpW\n7J:},y)
/Next 286 0 R
/Prev 290 0 R
/Parent 277 0 R
/A 291 0 R
>>
endobj
289 0 obj
<<
/S /GoTo
/D [ 118 0 R /XYZ 79 794 null ]
>>
endobj
290 0 obj
<<
/Title (q3i[T.b=a)
/Next 288 0 R
/Prev 292 0 R
/Parent 277 0 R
/A 293 0 R
>>
endobj
291 0 obj
<<
/S /GoTo
/D [ 112 0 R /XYZ 79 794 null ]
>>
endobj
292 0 obj
<<
/Title ($Ni*Ru\))
/Next 290 0 R
/Prev 294 0 R
/Parent 277 0 R
/A 295 0 R
>>
endobj
293 0 obj
<<
/S /GoTo
/D [ 81 0 R /XYZ 79 794 null ]
>>
endobj
294 0 obj
<<
/Title ("yu!;4sLs)
/Next 292 0 R
/Prev 296 0 R
/Parent 277 0 R
/A 297 0 R
>>
endobj
295 0 obj
<<
/S /GoTo
/D [ 75 0 R /XYZ 79 794 null ]
>>
endobj
296 0 obj
<<
/Title (b2C11P\rqI)
/Next 294 0 R
/Prev 298 0 R
/Parent 277 0 R
/A 299 0 R
>>
endobj
297 0 obj
<<
/S /GoTo
/D [ 69 0 R /XYZ 79 794 null ]
>>
endobj
298 0 obj
<<
/Title (,[\("7HU$)
/Next 296 0 R
/Prev 300 0 R
/Parent 277 0 R
/A 301 0 R
>>
endobj
299 0 obj
<<
/S /GoTo
/D [ 63 0 R /XYZ -51 794 null ]
>>
endobj
300 0 obj
<<
/Title (T8hy)
/A 302 0 R
/Next 298 0 R
/Prev 278 0 R
/Parent 277 0 R
>>
endobj
301 0 obj
<<
/S /GoTo
/D [ 49 0 R /XYZ 79 794 null ]
>>
endobj
302 0 obj
<<
/S /GoTo
/D [ 49 0 R /XYZ 79 794 null ]
>>
endobj
303 0 obj
<<
/S /GoTo
/D [ 10 0 R /XYZ -51 797 null ]
>>
endobj
304 0 obj
<<
/ProcSet [ /PDF /Text /ImageC ]
/Font << /F2 307 0 R >>
/XObject << /Im1 309 0 R >>
/ExtGState << /GS1 308 0 R >>
>>
endobj
305 0 obj
<< /Length 185 /Filter /FlateDecode >>
stream
Ou4Ui8+/
y`Z&gS+*C& [''#*k(i)M|DQhP:"r;c8uel+M-sJB
v8$s3&xSaKV] Fbd@ti*-i
b{SCMYVfl*u4 | Ultimately, steam traps require a maintenance program to determine if they are working to their full potential. We have found out what P4 is and we calculated for this example, lets say a 1000 pounds per hour condensate capacity. Do you have experience and expertise with the topics mentioned in this content?
The floating device is connected by mechanical linkage to a discharge valve that opens or closes based on the fluid level in the trap. of Energy (DOE), approximately 20% of steam leaving a boiler plant could be lost due to leaking steam traps in steam systems without a preventative maintenance program. David Grassl is a mechanical engineer at Ring & DuChateau, and an adjunct professor in the civil and architectural engineering and construction management department at the Milwaukee School of Engineering. Know the condensate pressure, so you get the correct differential.

As steam leaks through steam traps, the steam is condensed by conductive losses in the piping system as it returns to the condensate receiver or is vented out the receiver and lost, many times without detection. You also have the option to opt-out of these cookies. Failed steam traps can have a spiraling cost impact above and beyond wasted steam, including increased feedwater costs, additional chemical treatment and make-up water, and higher blowdown requirements. Determine the maximum pressure on the steam line supplying the process. When ordering replacement lever and seat assemblies, specify model and operating pressure.

0000001290 00000 n
By David Grassl, PE, Ring & DuChateau LLP, Milwaukee, By using this website, you agree to our use of cookies. The most difficult item in a steam system survey is to determine if steam traps are operating correctly or are faulty and wasting energy.
fte float steam ftes options Mechanical traps discharge condensate at the same temperature as steam, which makes them great for areas of high heat transfer at equipment such as heating coils or heat exchangers. There are conditions when lifting condensate is acceptable, but it should be avoided wherever possible to reduce backpressure on the traps. Noncondensable gases such as oxygen and carbon dioxide produce carbonic acid, scale, and corrosion, creating conditions that promote leaks within the distribution system. It follows, of course, that a larger size orifice would allow the trap to have a greater discharge capacity. Choosing the Right Type of Filtration Centrifuge, Hybrid membrane separates CO2 with both high permeability and selectivity, Biodegradable corn-based adhesive is non-toxic, with tunable properties, Commercial debut for sand-based thermal-energy storage, A more-sensitive way to differentiate chiral compounds, Upcycling of waste ABS into 3D-printable material with enhanced properties, Extending the operating temperature of biological phosphorus removal, Limpet tooth inspires strongest biomaterial, Biosynthesis of renewable, high-energy-density, cyclopropane-based fuels, Tower Doctor: X-Raying The Patient: Gamma Scanning Vapor Cross-Flow Channeling, Ethernet-APL: The Future of Field Connectivity, Facts At Your Fingertips: Heat-Transfer Fluid System Venting, Magnetic-Drive Positive-Displacement Pumps for Chemical Processing Applications, Steps to Improve Safety Challenges in Hazardous Environments, ChemChronicles: 'Eye it Before You Buy It,' The Invention of Cellophane, Facts at your Fingertips: Clean-in-Place (CIP) Systems, A condensate-recovery system for high-temperature operations, Inverted-bucket steam traps for high pressures, This steam-trap monitor has ISA100 Wireless certification, How Selective Catalytic Reduction Can Reduce NOx in Modern Power Stations, Casting Process Engineer - Aludyne - Montague, MI, Wafer Fab Process Engineer Broadcom Optical Systems Division (OSD) - Broadcom - , PA, Senior Process Engineer - Fluor - Mannheim, Germany, Process Engineer (m/w/d) - Fluor - Mannheim, Germany, Process Engineer - Fluor - Tarragona, Spain.
traps thermostatic steam wt4000 Steam traps are classified based on the physical process that allows them to open and close; they generally fall into one of the categories described below, while some traps may utilize a combination of two categories. Unintentional operation is elevating the condensate overhead into the pipe rack.

We have a 50-psi differential across a steam trap.
inverted steam bucket ib traps trap watsonmcdaniel Also available are replacement screens, gaskets and buckets. Out in the real world, plants need to have pressure gauges at the outlet of the steam trap, so we know what P5 is. In any case, the condensate piping to the steam trap should be no smaller than the designed condensate outlet of the process equipment, and the outlet of the steam trap should be the discharge pipe size of the branch piping to the condensate main to maximize gravity flow to the condensate return main piping. The PDF document will be sent to the email address specified. Example, 100 psi operating steam line does not mean 100 psi at the control valve. 0000004278 00000 n
Out of these, the cookies that are categorized as necessary are stored on your browser as they are essential for the working of basic functionalities of the website. At the bottom of the drip leg, a drain valve should be provided to remove condensate, and isolation valves and unions are recommended at the inlet and outlet of the steam trap to simplify trap removal. 0000004742 00000 n
. Figure 4demonstrates an installation with the appropriate top takeoffs for condensate piping.

Although building services can use high-pressure steam piping, the most common locations for ASME B31.1 are within industrial plants or central/district steam heating plants. Certain articles contain the author's personal recommendations only. Important facts to remember: Obtaining efficient and reliable steam trap operation. Straight sections of piping should also receive drip traps at regular intervals depending on the pitch of the piping. 0, Example:
Ill go across the top here and Im looking for that differential. Necessary cookies are absolutely essential for the website to function properly. For example, the orifice diameters available for the J3X Free Float steam trap are only approx. As the fluid within the trap changes, static and dynamic pressures change based on velocity to operate the discharge valve. For example, with a pressure differential of 0.2 MPaG [30 psi] ], a 2-3mm [ inch) orifice can discharge approximately 350 kg/h [770 lb/h] of condensate. We took the capacity times the sizing factor. The operating pressure to the process as you can see is at 75 psi. For example, based on the size of the steam trap and orifice size, one can estimate the amount of live steam lost through the trap.

My name is Kelly Paffel. While a Free Float steam trap with a nominal connection size of 15mm [ inch] is typically connected to piping with an inner diameter of 15mm [ inch], the diameter of the orifice may only be around 2-3mm [ inch] or less. 0000003174 00000 n
All heat transfer components have a pressure drop. 0000003715 00000 n
0000002729 00000 n
Banner Engineering TLF100 PRO flush mount tower light, SmartlockPro Self-Test GFCI Combination USB Type A/Type C In-Wall Charger. trailer
<<
/Size 312
/Info 265 0 R
/Encrypt 274 0 R
/Root 273 0 R
/Prev 1143009
/ID[<4f7aff5ea1b7af363ec59855866f3c9f><4f7aff5ea1b7af363ec59855866f3c9f>]
>>
startxref
0
%%EOF
273 0 obj
<<
/Type /Catalog
/Pages 264 0 R
/Outlines 277 0 R
/PageMode /UseOutlines
/OpenAction 275 0 R
>>
endobj
274 0 obj
<<
/Filter /Standard
/V 1
/R 2
/O ( UV.`Dz-#_m_}g)
/U (.&eSL+4Pec_$].s)
/P -12
>>
endobj
275 0 obj
<<
/S /GoTo
/D [ 276 0 R /FitH -32768 ]
>>
endobj
310 0 obj
<< /S 656 /T 840 /O 926 /Filter /FlateDecode /Length 311 0 R >>
stream
Decrease SizeIncrease Size per 10 ft to ensure adequate condensate removal. This represents a considerable amount of wasted dollars in energy production. 0000003839 00000 n
However, this would require a proportionally larger size float for the same pressure differential, which increases the size of the trap body. Piping that pitches in the direction of flow should receive drip traps every 200 to 300 ft, and piping that pitches opposite the direction of flow should receive drip traps every 150 ft3 according to the ASHRAE HandbookHVAC Applications. At the inlet to the steam trap, a strainer with a blowdown valve will provide the ability to remove any scale, dirt, and debris in the piping system and allow an operator to depressurize the steam trap for maintenance. Subtract the heat transfer pressure drop from the steam control valve outlet pressure to determine the inlet pressure to the steam trap. Please stop by and look at our new website, we have a tremendous amount of information up there.
trap steam The most common type of thermodynamic trap is a disc type where the disc is the only moving part. %PDF-1.3
%
All steam traps should be located below the device they serve to allow condensate to be removed by gravity and not rely on pressure or velocity. The recommended vertical length of the drip leg should be 28 in. 0000002375 00000 n
In all cases, the steam trap must be located with maintenance in mind in an accessible location, as an inaccessible steam trap may be forgotten for years. The thing about that is thats significantly different than looking at 75 psi for the inlet pressure, theres a 25-psi difference and that can have a significant impact on the steam trap capacity. The operating pressure at the inlet to the control valve was 75 psi, inlet steam pressure of the steam trap, we said 50 psi. The maximum pressure is determined by the safety valve setting.
The other thing to remember; there can be back pressure on to the condensate system and a high percentage of steam trap application will have pressure in the discharge side of the steam trap and that pressure may be unintentional or deliberately produced by the design of the system. This is because although piping is generally sized for two-phase flow (condensate with steam vapor), the orifice only needs to be sized for the condensate volume. Click here to start this process. Application: 100 lbs/hr at 75 PSIG working pressure and 2 PSI differential pressure
RELIANCE ON ANY INFORMATION SUPPLIED IN THIS PUBLICATION IS SOLELY AT YOUR OWN RISK.